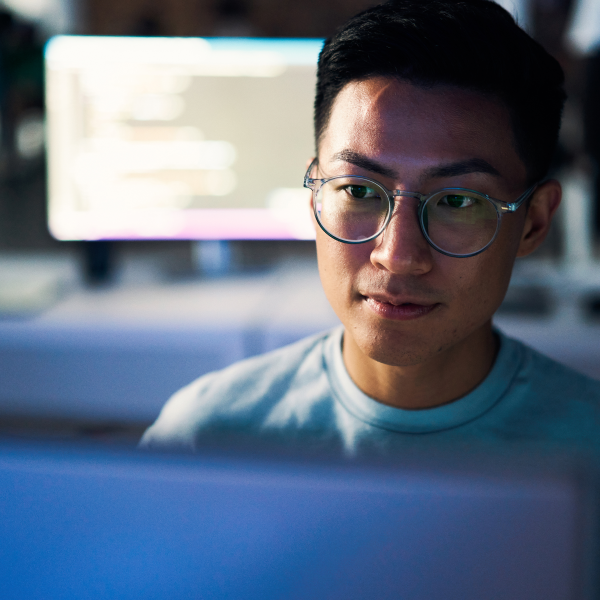
G&J Pepsi profit rises by $30 million with Microsoft Dynamics 365
This article is contributed. See the original author and article here.
At Microsoft, we don’t see ourselves as a vendor. When it comes to our customers, we want to be seen as partners—and as trusted advocates. Today, we want to share a story about how Microsoft can help customers take the long view when it comes to transforming their businesses and adapting to the ever-changing needs of their industries and markets. In 2021, facing an uncertain post-pandemic economy, G&J Pepsi embarked on a transformation journey to maximize customer service, revenue, and cost savings by implementing solutions including Microsoft Dynamics 365 Field Service, Microsoft Dynamics 365 Remote Assist, Microsoft Dynamics 365 Sales, and other Microsoft technologies. Since then, it has continued to adapt and adopt solutions like Microsoft Copilot to position itself for future growth and continued success in a competitive landscape.
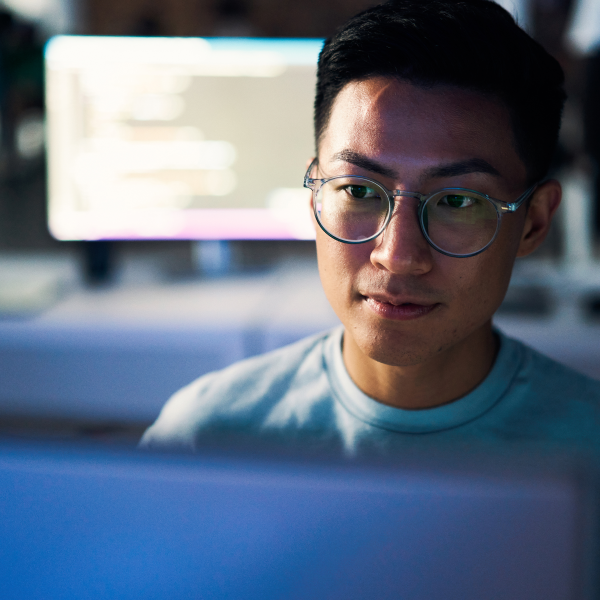
Dynamics 365 Field Service
Adapt and innovate with intelligent CRM and ERP business applications.
G&J Pepsi is always striving to innovate and provide better services for its customers. As the largest family-owned and operated independent U.S. Pepsi franchise bottler, it’s a respected leader in its industry. Supplying Pepsi and alliance products such as Starbucks, Gatorade, and Dr. Pepper to thousands of customers in Central and Southern Ohio and Eastern Kentucky, G&J Pepsi covers manufacturing, warehousing, distribution, trucking, digital print, and more. It produces, bottles, markets, sells, and distributes beverages consumed on-premises—restaurants, schools, entertainment complexes—as well as those purchased in retail outlets.
Breaking down siloes for a better customer view
In 2021, the company’s sales, field service, and other customer interactions were siloed. This meant that sales had no visibility into when a new customer might have its equipment installed, while field service technicians had no insights into a customer’s hours of operations, key contacts, or equipment needs. Customer information was stored in a mix of Excel spreadsheets, hand-written notes, and batch systems. In addition, employees across the service chain from sales to field service had no common platform for communicating and sharing information.
G&J Pepsi adopted Dynamics 365 Sales and Dynamics 365 Field Service to create a customer engagement management (CEM) platform, so it could accelerate its end-to-end customer journey by unifying cross-functional support and removing barriers to customer visibility. The CEM was a game-changer, especially because it provided real-time visibility into customers that sales, field service, and leadership never had before.
For field service operations, G&J Pepsi’s data resides in Microsoft Dataverse and is accessed through Dynamics 365 Field Service. Completing certain actions within Microsoft Dynamics 365 triggers a Microsoft Power Automate flow to kick off another process. For example, a business development representative (BDR) requesting a piece of equipment for a new customer triggers the creation of a new work order, which moves through equipment prep to scheduling a field technician for installation. Using built-in Dynamics 365 capabilities, a scheduler can assign best resources to a work order by looking across service locations instead of only selecting from a smaller subset of available technicians. Field service technicians use the Field Service mobile app’s built-in map and routing features to optimize travel time and status flags to indicate if they are on-site or traveling. Field techs can also access all the pertinent customer information in the mobile app: service tasks, customer details, product needs, and so on. And with minimal development effort using Microsoft Power Apps, G&J Pepsi extended the mobile app so that field technicians can generate service reports at the customer site and instantly email them to other departments as needed.
Simplifying and enhancing business processes for better employee experiences
G&J Pepsi has a digital transformation and business process team that selectively built their DevOps skills to simplify their application environment and processes using the Microsoft suite of services. In addition, they included frontline employees like service agents and field technicians through all stages of development, testing, and deployment. For example, the company’s Equipment Move Operation (EMO) process, which it performs about 10,000 times a year, had 17 manual steps—170,000 manual touchpoints annually. With Dynamics 365 and Power Automate, it automated that process, reducing a four-day event with 17 manual tasks down to a process that now takes about a minute. With these new processes, existing field technicians immediately felt more efficient and productive during customer visits, and G&J has found that it’s also attracting new talent because it provides modern tools and information flows that result in a better working environment.
Accelerating customer response times and improving first-time fix rates
The CEM platform based on Dynamics 365 Field Service and Dynamics 365 Sales has dramatically transformed G&J Pepsi’s operational workflow, cutting down paperwork processing from weeks to mere seconds and significantly boosting efficiency. The unified systems give salespeople, service agents, and field technicians immediate access to critical information, so they spend less time retrieving data and can focus on delivering exceptional customer service. Dynamics 365 Field Service has especially improved efficiency for onsite workers through smart scheduling and automation, and its interoperation with Pepsi’s other backend services helps it provide service agents with real-time updates and better stock management, enabling more effective customer service and streamlining operations. In addition, the interoperability of Field Service with Microsoft Teams has reduced email and simplified collaboration across the service chain, enabling service agents and field technicians to quickly locate information and subject matter experts, leading to faster resolution times.
Adopting Field Service also helped G&J Pepsi improve mobile operations for field technicians because now they no longer need to return to the office or another physical location with dial-up to sync data with backend systems. Now, dispatchers can adjust service schedules in real time, so technicians can quickly address urgent issues, such as water leaks at major accounts. The Field Service mobile app has also enhanced efficiency by improving communication between field technicians and dispatchers and enabling them to manage tasks, like work order management and inventory control, on the fly. The Field Service mobile app also uses cellular technology to auto-update inventory as technicians use parts, avoiding manual entries and speeding up restocking processes. These changes have profoundly improved the responsiveness of field service technicians, resulting in better customer service. Overall, G&J Pepsi is experiencing better first-time fix rates, reducing the need for return visits, which in turn saves costs related to time, mileage, and fuel. It also helps G&J Pepsi achieve greater operational efficiencies and improve overall customer satisfaction by ensuring technicians have the necessary parts and information to complete jobs effectively on the very first visit.
Benefitting from streamlined operations—and $30 million ROI over three years
By giving salespeople, service agents, and field technicians instant access to sales history, equipment details, schedules, parts, and pricing, G&J Pepsi has streamlined operations and enhanced customer service. Before implementing its CEM platform based on Dynamics 365, the company was experiencing a $9 million yearly loss due to siloed information, outdated manual processes, and inefficient communications and collaboration. But over its three-year journey with Dynamics 365, G&J Pepsi has achieved a $30 million ROI, amounting to a total of $57 million in cost savings over the same period. In addition, simplifying processes and using technology for better data access and automation led to a 10 point increase in market share in the on-premises sector, significantly outperforming the norm of 0.5 point annual growth. And with its data residing in the Dataverse, G&J has been able to gain access to real-time insights that have transformed its operations. Overall, using Dynamics 365 and Power Automate, it has streamlined 180,000 manual steps that used to take seven to 10 days each down to 35 seconds.
Embracing a future powered by AI through Microsoft Copilot and Microsoft Azure
Moving forward, G&J Pepsi is excited to explore the possibilities of using Microsoft Copilot to help frontline employees address real-world challenges, like optimizing scheduling and service flows based on data analysis. It plans to employ technologists and AI experts to help drive awareness and adoption of Copilot capabilities to help transform the customer experience. Microsoft tools like Copilot, Microsoft Azure AI, and Power Automate will also play a big role in helping G&J enhance its enterprise resource planning strategy and growth by creating a digital thread through its daily business operations to help succeed daily.
“We truly see Microsoft as an organization that is tied to the entire success of G&J Pepsi, not just the entire success of the department, but as a true collaborator, where we’re getting our voice heard on some of the challenges and opportunities that we have with the products. Not just with Copilot, but with all the platforms, from Dynamics 365 to Microsoft 365 to Azure.”
Brian Balzer, Executive Vice President of Digital Technology & Business Transformation, G&J Pepsi-Cola Bottlers.
Read more about G&J Pepsi’s transformation here:
The post G&J Pepsi profit rises by $30 million with Microsoft Dynamics 365 appeared first on Microsoft Dynamics 365 Blog.
Brought to you by Dr. Ware, Microsoft Office 365 Silver Partner, Charleston SC.
Recent Comments